More and more modular control components are used in modern cars, and communication is realized by CAN-BUS vehicle intelligent network control system, which not only can greatly reduce the traditional circuit, but also makes the data transmission fast and accurate, and is also more convenient for diagnosis. And repair.
This article refers to the address: http://
Jiangling's new generation of Transit - the module control components used on the V348 include PCM, RCM, PJB, PAM, PATS, ABS/ESP, SAS and HEC (see Figure 1 for the vehicle control module). These modules communicate via the CAN bus. diagnosis.
In the process of assembly of the whole vehicle, we adopted VCATS technology to realize data downloading, detection and fault diagnosis of the vehicle electronic control system to test the working condition of each module, and find out the faults in time to ensure that the electronic control system can be accurate after the vehicle goes offline. Stable operation, qualified factory.
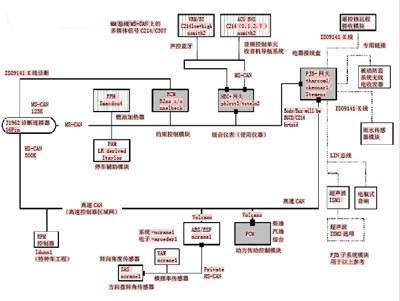
Figure 1 Jiangling new generation Transit vehicle control module layout
VCATS system composition
“VCATS†is the abbreviation of “Vehicle and Configuration Test Solutionsâ€, which is the vehicle setting and testing system. It is mainly composed of the following devices: 1 server, several test stations (three test stations set by our company), 1 Handheld operating device (HHU) and a test result printer. Figure 2 shows the composition and process of the VCATS system.
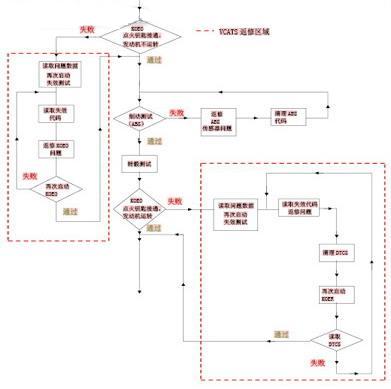
Figure 2 VCATS process
The server is used to decode the vehicle parameters and the vehicle ID and send the parameters of the vehicle to the test station. In order to effectively reduce the system cost, the server also takes into account the function of the maintenance area, while accepting the vehicle test data transmitted from the test station and storing it in the database. The transmission and acceptance of data is done using a wireless network.
The test station is installed at different stations to test the operating status and parameters of the vehicle under various working conditions.
The handheld operating device is equipped with a bar code reading device and an LCD display, which displays the test program information in real time and prompts the operator with the operation steps. The unit is also equipped with a keyboard that allows the operator to enter commands and information as the test cycle proceeds. Communication between the handheld operating device and the test electrical box is accomplished via RF.
The vehicle interface device GNA 610 is connected to the vehicle diagnostic connector (OBD) by wires, and the connection pin device between the GNA 610 and the test electrical box is connected to the communication interface by RF.
Each test station is equipped with a test result printer that provides a report printout of vehicle test failures.
In addition, the server in the repair area can also remotely monitor other test stations.
In addition to the above, the VCATS system option includes Quality, a suite of software that specifically supports FTT (First Time Through) and analyzes data results.
VCATS is installed in the network. Its main advantage is that the operator can remotely control VCATS access, find DTCs in time and provide fault causes and solutions.
VCATS process introduction
Our company's VCATS system test process steps are divided into pre-roll (Pre-Roll) (see Figure 3), drum (Roll), post-roll (Post-Roll) and rework station Repair Bay (see Figure 4). The specific process content of each step is as follows:
Test station 1 (ie Pre-Roll station): is the last station installed in the final assembly line, also known as "KOEO (Key Off Engine Off)", that is, the ignition key is turned on, and the engine is not started, use Complete data entry and programming of the vehicle module and perform electrical and functional integrity diagnosis of the vehicle. This phase should be completed before the vehicle completes the final station after assembly and the engine is first started.
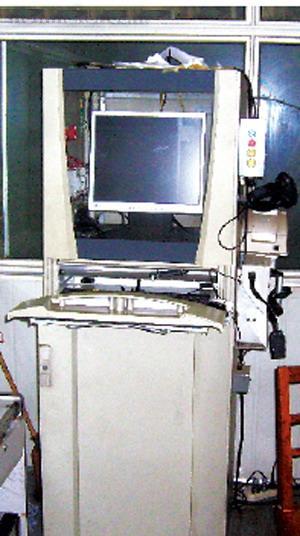
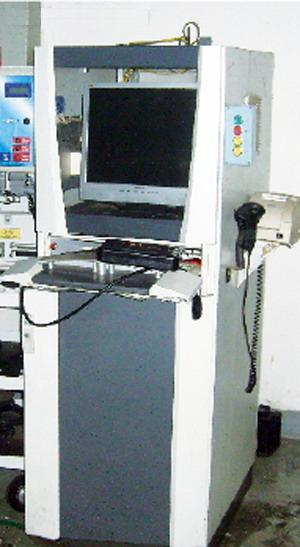
Figure 3 Pre-roll VCATS device
In our company, we complete the test in two steps in different positions: the first step is to carry out the initialization of the vehicle module and the preliminary electrical inspection, check the result but not the fault code; the second step detects the fault code and according to the fault code. Prompt for fault clearing.
There is an integrated server control cabinet at this station (with three PC hosts, which can be used for ECU initialization program execution, static electrical detection, acceptance of test data at various stages, and data storage). This station is also used for VCATS operations in the repair area.
Test station 2 (ie Roll station): It is tested on the ABS drum table to detect the dynamic output value of the ECU control module during dynamic driving. The test value can be used as the judgment of the working condition of each module. The stored data comparison can reflect the difference in the delivery status of each module and the cause analysis of the problem vehicle, such as PCM, TCM, EGR, etc.
Test station 3 (ie Post-Roll station): Also known as "KOER", the ignition key is turned on and the engine is running. This phase is to monitor the output values ​​of modules with dynamic functionality, such as PCM, ABS modules, and TCM. The ECOS test is also integrated into the VCATS test after the drum, they share a set of hardware
The maintenance area VCATS (ie Repair Bay) server has the test functions of test station 1 and test station 3. Within test station 1 or test station 3, specific vehicle tests or module configurations can be done separately. Test result data from test stations 1 and 2 can be observed and the record is automatically updated after the repair and retest is completed.
Conclusion
Modern vehicles are increasingly using electronic controls, and module control technology is also widely used. The VCATS system is used to test the working condition of each module in the assembly process, to eliminate the faults in the process, and to ensure the accurate and stable operation of the vehicle control module, which is a reliable guarantee for the performance and quality of the vehicle. With the development and advancement of automotive electronics technology, VCATS processes and technologies need to be continuously improved and improved.
Paper wrapped winding wire is made up of bare from oxygen free Copper Rod or electrical aluminum rod by drawing or extruding processing and wrapped by insulation materials.paper covered single wire , with insulation wrapping in the outside layer
As per Conductor Material:Copper , aluminum
As per Inner Conductor: Paper wrapped bare
Insulation thickness:Double paper covered (DPC) orTriple Paper Covered (TPC) ,According to Customer`s requirements
Packaging DetailsInner packing : Wooden bobbin
Outer packing : Wooden pallet and stretch film
Or according to our custormers' requirements
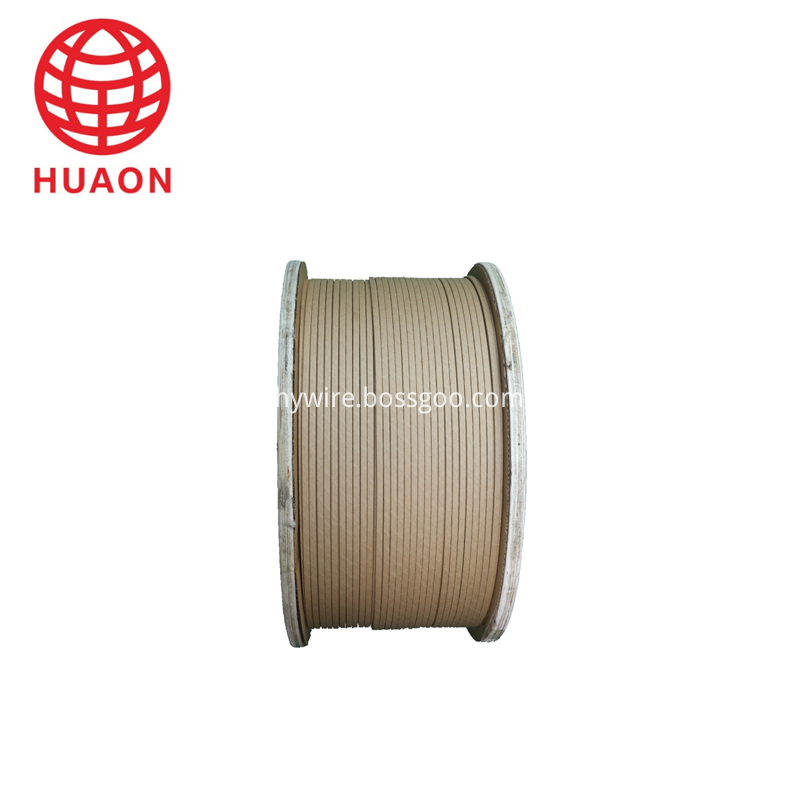
Conductor of Paper wrapped wire
Bare Wire Round Wire:Φ1.00 mm-Φ5.00 mm
Rectangular Wire thickness a:1.00 mm-5.60 mm
Width b:2.00 mm-16.00 mm
Conductor of Composite wires
Max wrapping layers once: 24 layers for Paper Covered Wire
4 layers per wire and 16 layers outside for composite wires
We could offer products of special requirements on conductor size, insulation layer thickness, or wire number of the composite.
Paper Covered Flat Aluminium Wire
Electrical Wire,Paper Covered Flat Aluminium Wire,Covered Magnet Aluminum Wire,Covered Magnet Aluminum Winding
HENAN HUAYANG COPPER GROUP CO.,LTD , https://www.huaonwire.com